One of the reasons we ran a trial run of the Project X Katana rather than just offer it as a new custom sword available all year round is to make sure the customization process goes smoothly and to identify and bottlenecks or delays in production.
And indeed, it appears it was a wise choice, as to date only 50% of the orders placed in late May came in on time, the other 50% are now running a couple of weeks behind the original maximum quoted lead time..
Why?
Well, there are a couple of very good reasons.
The first is that laminated swords generally have a high failure rate. Its a complex procedure – made even harder because of all the various lamination methods, Soshu Kitae is by far the most complex..
To make one good sword, it usually takes 4-6 attempts. Many fail at the heat treat and hardening stages, for a when a dreaded ‘ping’ sound occurs, the blade has cracked and cannot be salvaged – the smiths need to start from the very beginning again.
However just because a sword survived the heat treat okay doesn’t mean that its out of the woods. Many flaws are only revealed during the polishing stage – sometimes after 4-5 hours of hard work has gone into the blade.. In these cases, either the lamination line or the hamon have run off the edge of the blade (fatal flaw) or there are some grind marks or scratches that occurred during the grinding phase before heat treatment that are too deep to completely polish out.
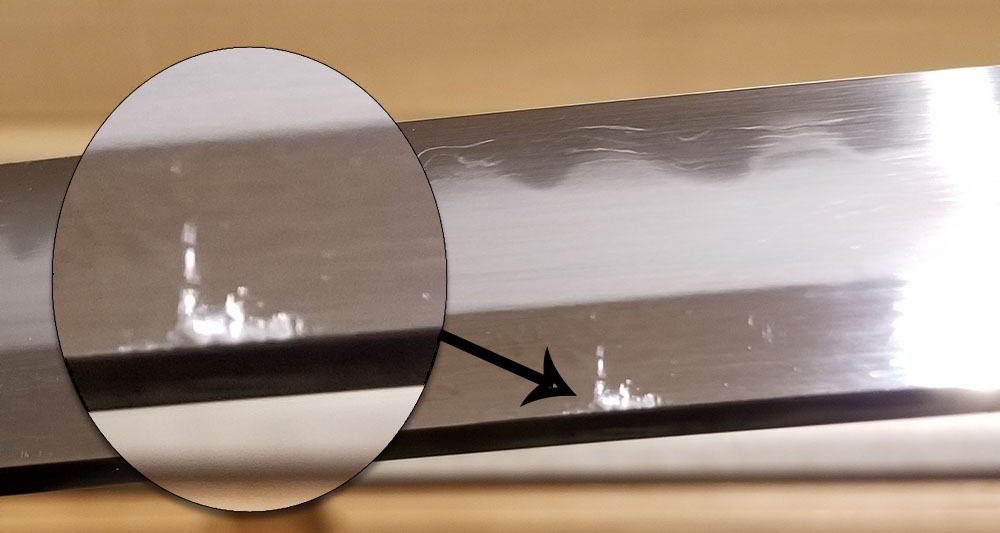
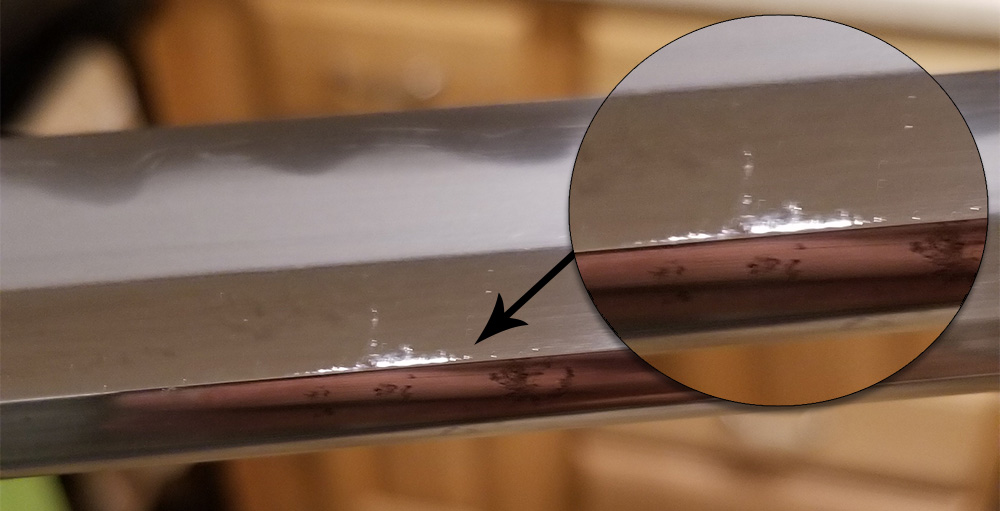
When this happens, there are two options – either abandon the blade and start again or keep going to try to get it as smooth as possible, as it is a non-fatal flaw.
Flaws like these are called ‘kizu’ and even high end Nihonto made in Japan may have ‘kizu’ that are deemed to be fatal (i.e. make the sword dangerous to use) or non-fatal (just not so pretty to look at). You can find an excellent list of the most common ‘kizu’ that will occur with a Katana here on Richard Stein’s excellent Japanese Sword Index.
For Project X Japanese, we subject our swords to a standard above and beyond even what is considered acceptable for a $10,000 Nihonto. None of these flaws are acceptable to us – but sadly there is a long line of eBay sellers and other local suppliers who are quite happy to snap up the rejects at bargain basement prices and flog them off as brand new, quality blades rather than scratch and dent them as they should.. Indeed, they even go so far as to sell swords that were failed heat treatment as functional cutters – and sadly as a rejected sword is no longer our property, there isn’t anything we can do about it..
Anyway, the point of this post is to explain why these swords take a bit longer than usual to make as its often the case that the flaws are not found until several days of hard work have already been applied – so moving forward we have revised the lead time from 4-6 weeks to 3-4 MONTHS with some coming in slightly earlier and others slightly later, but all in all considering just how much work goes into making them, even 3-4 months is something of a miracle..
Quality like this takes time..
Anyway, the swords that are awaiting completion will take another couple of weeks max before they are finished and we are ready to start a second trial run (along with a few new models including a Kogarasu) – so if you haven’t already, be sure to sign up to the Project X Newsletter to be notified when the next opportunity to get these opens up..
As you might expect, demand is pretty high for these swords and its very easy to miss the boat – so when the time comes, the faster you can secure your order the better..
P.S. In the spirit of full disclosure, I hate to admit it but the flaws you see above were on a sword that was sent to one of our customers.. It should go without saying that we kicked up quite a fuss with the forge about this, saying it is totally unacceptable for this line, and the sword in question is being remade for the customer and the point has been driven home – nothing but the VERY best is acceptable for Project X, and even flaws that are acceptable on Nihonto will not be tolerated here..